Tailor-made manufacturing.
It all depends on the right technology.
Different production techniques are used during production, depending on needs, requirements and material, including manufacturing with suction-blow technique, manipulation or 3D techniques. Our film contributions inform you about the different production techniques as well as about the experience we have from using different materials.
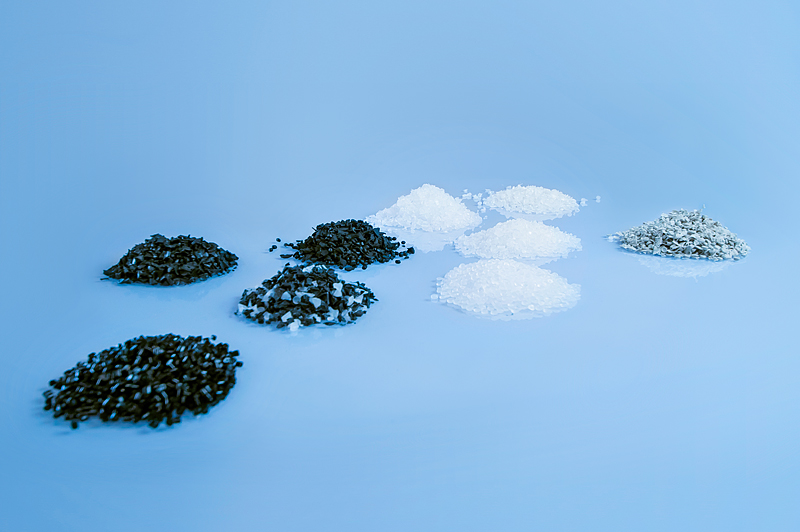
Conventional production
Advantages
Disadvantages
- Standard machines
- Affordable mould costs
- Short preparation and adjustment processes
Disadvantages
- Increased necessity for clamping force and plasticisation capacity
- Welding seams on blow-moulded part
- Work-intensive due to re-work on blow-moulded part
Production with manipulation
Advantages
Disadvantages
- 3D moulded parts
- Relatively short cycle times and good line-monitoring during shaping
- Larger design possibilities than in conventional processes
- Optimal use of materials
Disadvantages
- High tooling and maintenance costs on the blow-moulding tool
- Complex plant engineering with many special functions
- Restricted further processing possibilities with the blow-moulding tool
- Sometimes longer preparation and adjustment processes
Production with suction blow
Advantages
Disadvantages
- 3D mould parts
- Articles without welding seams and burrs
- Affordable mould costs
- Optimal use of materials
Disadvantages
- Restricted line monitoring in the blow mould
- Longer cycle times than with conventional production
- Necessity for special preparation of the blow-moulding plant
- Long preparation and adjustment processes
Production with 3D technique
Advantages
Disadvantages
- Complex 3D mould sizes
- Articles without welding seams and burrs
- Greater design margin (acute bends possible)
- Optimised use of material and affordable mould costs
Disadvantages
- Necessity for special machine with robots
- Uneven wall-thickness distribution
- Longer process times and restricted choice of materials
- Long preparation and adjustment processes